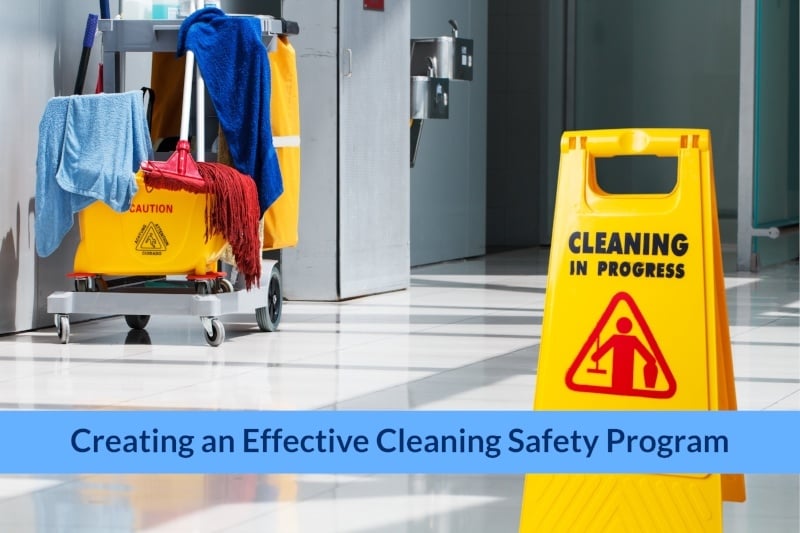
Creating and maintaining an effective cleaning safety program is essential for any cleaning operation. Over the past 20 years, “safety” has become an increasingly important topic within the cleaning industry. As a result, many cleaning operations have developed detailed safety programs that put significant emphasis on training and use of industry best practices. Does your cleaning operation have an effective cleaning safety program? What are the most essential components of such a program?
In this week’s Part 1 post we will review….
- Hazard Communication
- Bloodborne Pathogens
- Slip, Trip, Fall Prevention
Hazard Communication
The “Hazard Communication” portion of any cleaning safety program should be in compliance with the OSHA Hazard Communication Standard. The OSHA Standard is CFR 1910.1200. A safety program would address each of the following areas related to hazard communication:
- Labeling of Containers: The cleaning operation should verify that all hazardous materials are marked with the original labeling as received from the manufacturer. Labels should also be verified to contain all GHS requirements for product labeling (manufacturer name, emergency numbers, warnings, etc.)
- Safety Data Sheets (SDS): The cleaning safety program should clearly specify methods for receipt, storage, dissemination, and availability of SDS for all hazardous materials used by the cleaning operation.
- Employee Training: Proper training of employees is critical. The training should include anyone that works with, or that may be exposed to, hazardous materials. This training is typically conducted during the new employee orientation process. Training would include (but not be limited to): overview of OSHA Hazard Communication Standard, review and location of SDS, product labeling, health risks associated with all hazardous materials or chemicals, emergency procedures, etc.
Bloodborne Pathogens
Your cleaning safety program should include explicit instructions and procedures on how to handle spills that contain bloodborne pathogens. Those instructions should provide specific information as related to:
- Cleaning of spills on various surface types (concrete, wood, carpet, etc.)
- Procedures for post clean-up (hand-washing, proper disposal of waste and cleaning materials, etc.)
- Handling of incidents of exposure (emergency procedures, reporting of incidents, etc.)
- Training of employees who could be exposed to bloodborne pathogens. Protocols and safety measures to minimize risk of exposure. Location and proper use of Personal Protection Equipment (PPE).
Slip, Trip and Fall Prevention
Slips, trips, and falls are among the most frequent types of accidents within the workplace. These accidents result in significant loss of employee productivity, increased insurance premiums, and increased costs associated with replacement of employees. A cleaning safety program should address slip, trip, and fall preventive measures such as:
- Good housekeeping practices
- Proper footwear
- Rapid containment of spills
- Adequate lighting
- Slip resistant flooring in high-risk areas
An effective cleaning safety program would incorporate all of the above….and more.
Do you have a detailed safety training program in place? Let us know in the section for comments below.
And if you need a customized, cost-effective Service Solution for your business, let SMO help. Request a Customized Service Solution today.