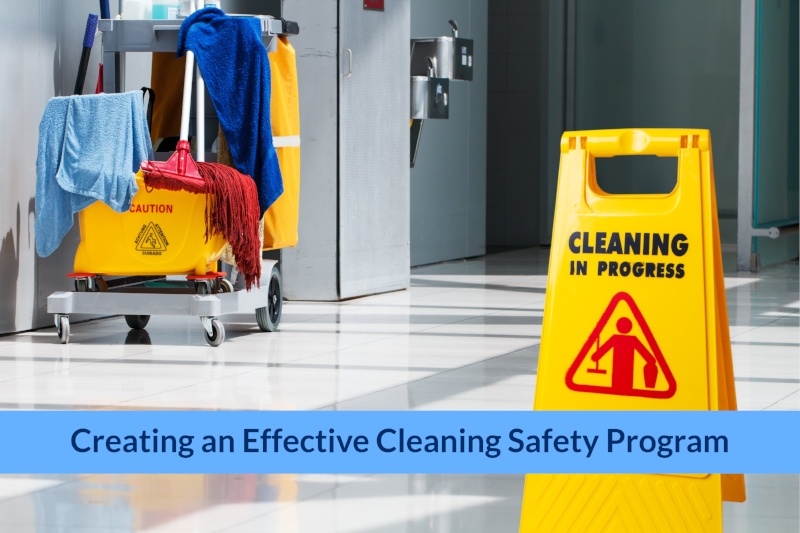
In last week’s post, Creating an Effective Cleaning Safety Program Pt 1, we reviewed three of the elements that should be addressed as part of any cleaning safety program. In that post we discussed: Hazard Communication, Bloodborne Pathogens, and Slip, Trip, and Fall Prevention. This week we will highlight the importance of:
- MOD Rates
- Safety Inspections
- “Safety Always” Mindset
MOD Rates
One of the overarching objectives of a cleaning safety program is to control MOD rates within the cleaning operation. MOD rate classifications are defined as follows:
- MOD Rate < 1.0: The operation is operating at a level that is safer than average.
- MOD Rate = 1.0: The operation has a safety record that is average.
- MOD Rate > 1.0: The operation is performing below average (i.e. greater “risk”).
Why is this important? Simply put, higher MOD rates result in significantly higher insurance premiums. Those higher premiums can impede the cleaning operation’s ability to maintain competitive pricing. Non-competitive pricing means lost business, decreased revenue, and diminished bottom-line results.
Safety Inspections
Safety Inspections are at the heart of the cleaning safety program. A robust safety inspection process provides the operation with tangible evidence as to whether or not its safety program is working. The safety inspection process should include:
- Training: Inspectors should be adequately trained on the inspection process. This would include training on inspection procedures, use of applicable tools and materials, and reporting of results.
- Inspection Frequencies: The cleaning safety program should clearly define the frequencies and schedules for the safety inspections. Areas that have been identified as higher risk should be inspected at closer intervals than low-risk areas.
- Reporting, Review, and Corrective Action: The inspection process should establish guidelines on how inspection results are to be documented, reported, and reviewed. The process should also contain a closed-loop corrective action process in which all instances of non-compliance are corrected, validated, and closed.
“Safety Always” Mindset
Within any organization “safety” is a mindset that must be actively encouraged and fostered. “Safety Always” must be an organizational value and mandate that is shared and supported throughout the entire cleaning operation (executives, managers, supervisors, cleaning operators, etc.). Creation and maintenance of this mindset can be facilitated via…
- Actively reporting on safety related issues within the operation: Posting of safety inspections results that are visible to all employees. This can be done via bulletin board, website, internal newsletters, etc. Rewarding outstanding performance in the area of safety compliance. Demonstrating actions that were taken to resolve reported safety issues.
- Establishment of “safety” programs and initiatives: Establish programs that involve folks from all parts of the organization. Use those programs to constantly reinforce the organization’s full commitment to safety. Use training and communication techniques that encourage full support across the entire operation.
The creation of a safe work environment for employees and clients is an imperative for any cleaning operation. The development of an effective cleaning safety program is the first step towards fulfillment of that objective.
How do you create a safe commercial cleaning environment for your employees and clients? Let us know in the section for comments below.
And if you need a customized, cost-effective Service Solution for your business, let SMO help. Request a Customized Service Solution today.